There are many different types of custom-made leather labels. Today we mainly explain the difference between debossed and embossed, and then introduce the other crafts of leather label. May give you new ideas for understanding it.
1.Debossed
This type of craft is most loved by customers and can be seen everywhere. All trademarks will have a lower base than leather labels.
A.In accordance with the design draft, the factory carved brass into the corresponding trademark, which is higher than the metal base. This is the copper mold of debossed. The copper mold is then heated to 130 ° C-180° C to stamp the leather. Finally make the desired leather label. This is the most common deboosed production process.
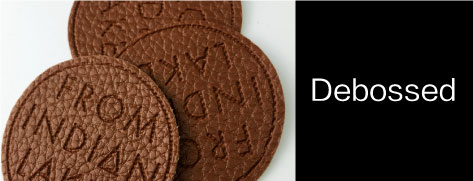
B.The second type of debossed process is foil stamping. Its process is a bit more complicated. Before pressing the leather, workers place a foil film on the leather, and the temperature rises to 130 ° C-180 ° C. After pressing, the logo will turn golden and the pattern debossed
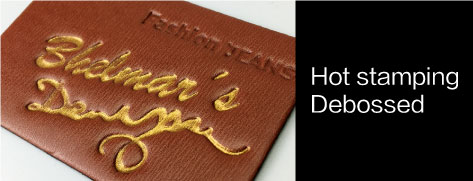
C. Print and debossed process. This is a composite process. First, we will print the trademark on the leather, then heat the copper mold, align it with the trademark, and then press it down to make a leather label. The products of this process will be very distinctive, but its disadvantage is that the position of the trademark indentation will not be exactly the same as the position of printing. There must be something slightly different.
2. Embossed
Its craft and debossed are reversed. After its process, the logo pattern is slightly higher than the base surface of the leather label.
A. According to the design draft, the factory carved brass into the corresponding trademark, which is a bit lower than the metal bottom. This is the copper mold of embossed. The copper mold is then heated to 130 ° C-180 ° C to heat the leather. Finally make the desired leather label. Most customers who want to be embossed are such processes.
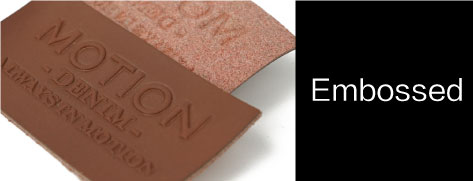
B.The second embossed process is foil stamping. Its process is a bit more complicated. Before pressing the leather, the worker places a foil film on the leather, and the temperature rises to 130 ° C-180 ° C. After pressing, the logo will turn golden and the pattern will be higher than the base surface. The design is very distinctive.
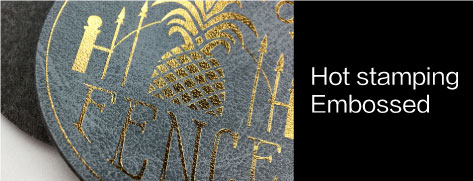
C. Print and embossed process. This is a composite process. First, we will print the trademark on the leather, then heat the copper mold, align it with the trademark, and then press it down to make a leather label. The products of this process will be very distinctive, but its disadvantage is that the position of the trademark indentation will not be exactly the same as the position of printing. There can be some slight difference.
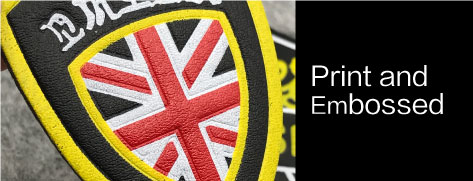
Pay attention to a very serious issue, many customers will confuse the debossed and embossed processes. And feel that most customers will consider the process of embossed as debossed. I hope customers can understand the difference after reading this article. Because most of the leather label trademarks are debossed, when customers consult us, we will be the first to recommend this process and show them pictures. Prevent this from going wrong!
3. Print
There are two types of printing processes.
A. Screen printing. It can only print monochrome logos. And it is manual. We will make a template, print it by hand, and cut out the leather label.
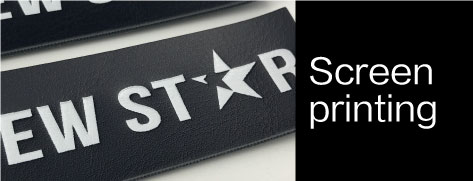
B. Color printing. The pattern is printed on the leather surface by a printing device. Because the leather is marked with its own original color, the color of most patterns will be affected by the original color. The color is not so bright. But also very popular with customers.
4. Embroidery
The embroidery process is really popular. Everyone only knows the embroidery patch. But few people know that leather labels can also be embroidered. Igingle has its own special embroidery machine to make embroidered leather labels. And customer feedback is pretty good. Some customers can use this process if they want to try something new. May be perfect for you.
5. Laser Engrave
It is the unusual laser engraving process.It's a laser device that use laser to touch the surface of the leather and carve out the pattern. The design will darken after laser garving, and logo is a bit rough when touch.
The advantages is the process speed is quick and can do several meters of patterns. But it looks not as attractive as stamping one.
Hope this article is helpful to you. If you have further questions, please contact us. Thank you!